Several factors influence load distribution in a bonfiglioli gearbox system, and engineers carefully consider these factors during the design and operation of the system. The goal is to achieve uniform loading on the gear teeth to ensure efficient power transmission and maximize the lifespan of the gearbox. Here are some key factors that influence load distribution in a gearbox:
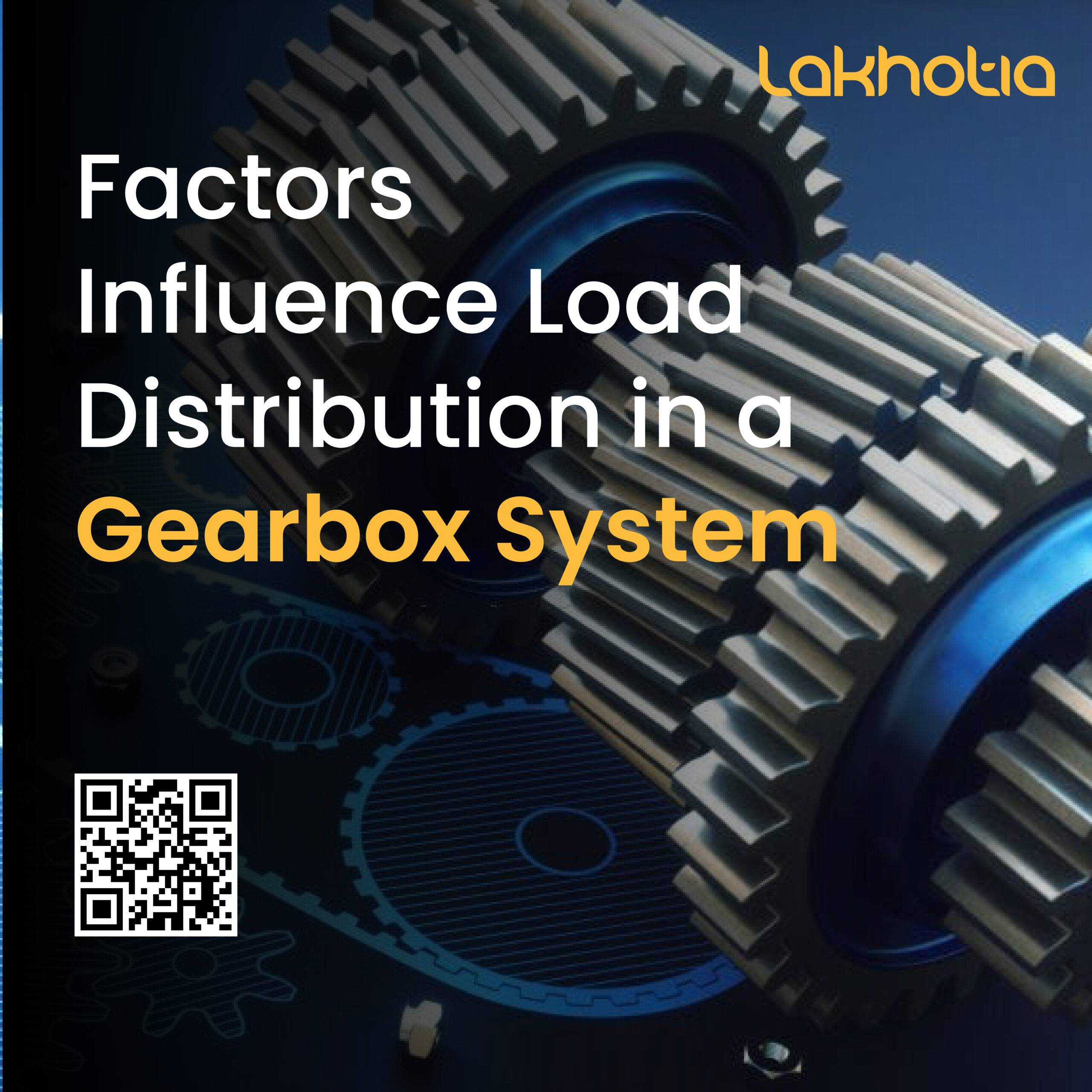
Tooth Profile: The design of the gear teeth, including the tooth profile (such as involute or cycloidal), significantly impacts load distribution. Properly designed teeth help distribute the load evenly across the entire tooth surface.
Helix Angle: The helix angle of helical gears affects the contact pattern and load distribution. Helical gears are designed to provide smoother engagement and distribute loads more evenly compared to spur gears.
Material Hardness: The hardness of the gear material affects its resistance to wear and fatigue. Proper material selection ensures that the gears can withstand the loads imposed on them without experiencing premature failure.
Lubricant Type and Quality: Proper lubrication is crucial for reducing friction and wear. The choice of lubricant, its viscosity, and the quality of lubrication are important factors in maintaining optimal load distribution.
Gearbox Alignment: Misalignment of gears can result in uneven loading and accelerated wear. Proper alignment during installation is essential to ensure that the gears mesh correctly and distribute loads uniformly.
Shaft Rigidity: The rigidity of the gearbox housing and supporting structures also affects load distribution. A rigid structure helps maintain proper gear alignment under load.
Torque and Power Levels: The amount of torque and power transmitted through the gearbox affects the magnitude of the loads on the gear teeth. Design considerations must account for the expected operational conditions.
Speed and Loading Variations: Changes in speed and loading conditions during operation can impact load distribution. The gearbox design should consider a range of operating conditions to ensure implementation under various scenarios.
Gear Manufacturing Tolerances: Precision in gear manufacturing is crucial for achieving uniform tooth geometry. Deviations from design specifications can lead to uneven loading and decreased efficiency.
Dynamic Loads: In some applications, dynamic loads, such as shocks or vibrations, can occur. The gearbox design should account for these dynamic effects to prevent excessive loading on specific gear teeth.
Engineers carefully analyze and balance these factors to optimize load distribution, ensuring that the gearbox operates efficiently and reliably over its intended service. Regular maintenance and monitoring are also important to address any changes in load distribution that may occur over time. Check out more products from lakhotia india.