Understanding Conveyor Belt Systems
it’s important to have a basic understanding of how conveyor belt systems work. Conveyor belts consist of two or more(drive or tail) pulleys with a continuous loop of material, known as the belt, rotating around them.
The powered pulley, known as the drive pulley, propels the belt, allowing it to carry materials from one point to another. Conveyor belts can be flat or inclined, depending on the application.
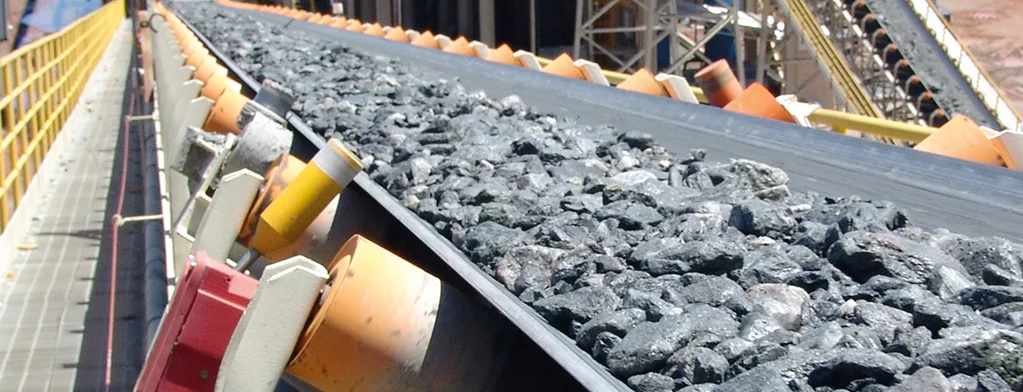
1. Belt Slippage
Belt slippage occurs when the belt loses traction and slips on the pulleys, leading to reduced efficiency and material spillage. This problem can arise due to factors such as inadequate belt tension, worn-out pulleys, or excessive load.
2. Belt Tracking Issues
Belt tracking problems occur when the belt deviates from its intended path, causing misalignment and potential damage to the belt and other conveyor components. This issue can be caused by uneven loading, improper installation, or worn-out tracking rollers.
3. Material Spillage
Material spillage is a common problem that can occur when the conveyor belt fails to contain the materials being transported, resulting in loss, waste, and potential safety hazards. Factors such as inadequate skirting, improper loading, or worn-out seals can contribute to material spillage.
4. Excessive Noise
Excessive noise from conveyor belts can indicate underlying problems such as misaligned components, worn-out bearings, or improper tensioning. It is important to address excessive noise to prevent further damage and maintain a safe and comfortable working environment.
5. Premature Wear and Tear
Premature wear and tear of conveyor belts can lead to frequent replacements, increased maintenance costs, and unexpected downtime. Factors such as abrasive materials, inadequate cleaning, or improper belt tensioning can contribute to accelerated wear and tear.
6. Conveyor Belt Damage
Conveyor belt damage can occur due to various reasons, including impact from heavy objects, sharp edges, or excessive tension. Damaged belts can compromise operational efficiency and pose safety risks.
7. Belt Alignment Problems
Belt alignment problems occur when the conveyor belt deviates from its intended path, causing uneven wear, mistracking, and potential damage to the belt and other components. Improper installation, worn-out rollers, or inadequate maintenance can contribute to belt alignment issues.
8. Belt Tension Irregularities
Inconsistent belt tension can result in poor performance, slippage, and premature wear. Factors such as improper tensioning techniques, mechanical issues, or changes in load can cause belt tension irregularities.
9. Motor Malfunctions
Motor malfunctions can disrupt the operation of conveyor belts, leading to unexpected downtime. Problems such as overheating, electrical failures, or mechanical issues can affect the motor’s performance and reliability.
10. Roller Issues
Conveyor belt rollers are essential components that support the belt and facilitate its movement. Issues such as misalignment, damaged rollers, or inadequate lubrication can affect the belt’s performance and lifespan.
11. Excessive Vibrations
Excessive vibrations in conveyor belts can indicate problems such as misalignment, unbalanced components, or mechanical issues. These vibrations can cause further damage if left unaddressed and may result in increased maintenance and reduced equipment lifespan.
12. Inadequate Belt Cleaning
Proper belt cleaning is crucial to prevent material buildup, belt slippage, and premature wear. Inadequate cleaning methods or lack of regular cleaning can contribute to reduced belt performance and increased maintenance requirements.
13. Jammed Rollers
Jammed rollers can disrupt the movement of the conveyor belt, leading to inefficiency and potential damage. Causes of jammed rollers include foreign objects, material buildup, or mechanical failures.
14. Overloading
Overloading the conveyor belt beyond its capacity can lead to belt damage, motor strain, and potential system failure. Proper load management and adherence to weight limits are crucial to prevent overloading.
15. Electrical Problems
Electrical problems, such as faulty wiring, damaged sensors, or motor control issues, can affect the operation of conveyor belts. Prompt identification and resolution of electrical issues are necessary to prevent safety hazards and operational disruptions.
However, like any other mechanical system, conveyor belts can experience various issues that can disrupt their operation and cause downtime, resulting in decreased productivity and increased costs.
Frequently Asked Questions
How often should conveyor belts be inspected?
Conveyor belts should be inspected regularly, ideally on a monthly basis. However, the frequency may vary depending on the specific application and operating conditions. High-intensity operations may require more frequent inspections.
What causes belt slippage?
Belt slippage can be caused by inadequate belt tension, worn-out pulleys, excessive load, or insufficient friction between the belt and pulleys. Addressing these factors can help prevent belt slippage.
How can excessive vibrations be reduced?
Excessive vibrations can be reduced by identifying the root cause, such as misalignment, unbalanced components, or mechanical issues, and taking appropriate corrective measures. This may involve realignment, component replacement, or vibration dampening techniques.
Are there any preventive measures to minimize material spillage?
Yes, several preventive measures can minimize material spillage, including proper skirting, sealing, and loading techniques. Installing effective containment systems, such as skirtboard seals or impact beds, can also help prevent material spillage.
Can I troubleshoot conveyor belt problems without professional assistance?
While some minor issues can be resolved by following troubleshooting guidelines, complex or safety-sensitive problems may require professional assistance. It is important to prioritize safety and consult with experts when needed.
Leave a Reply