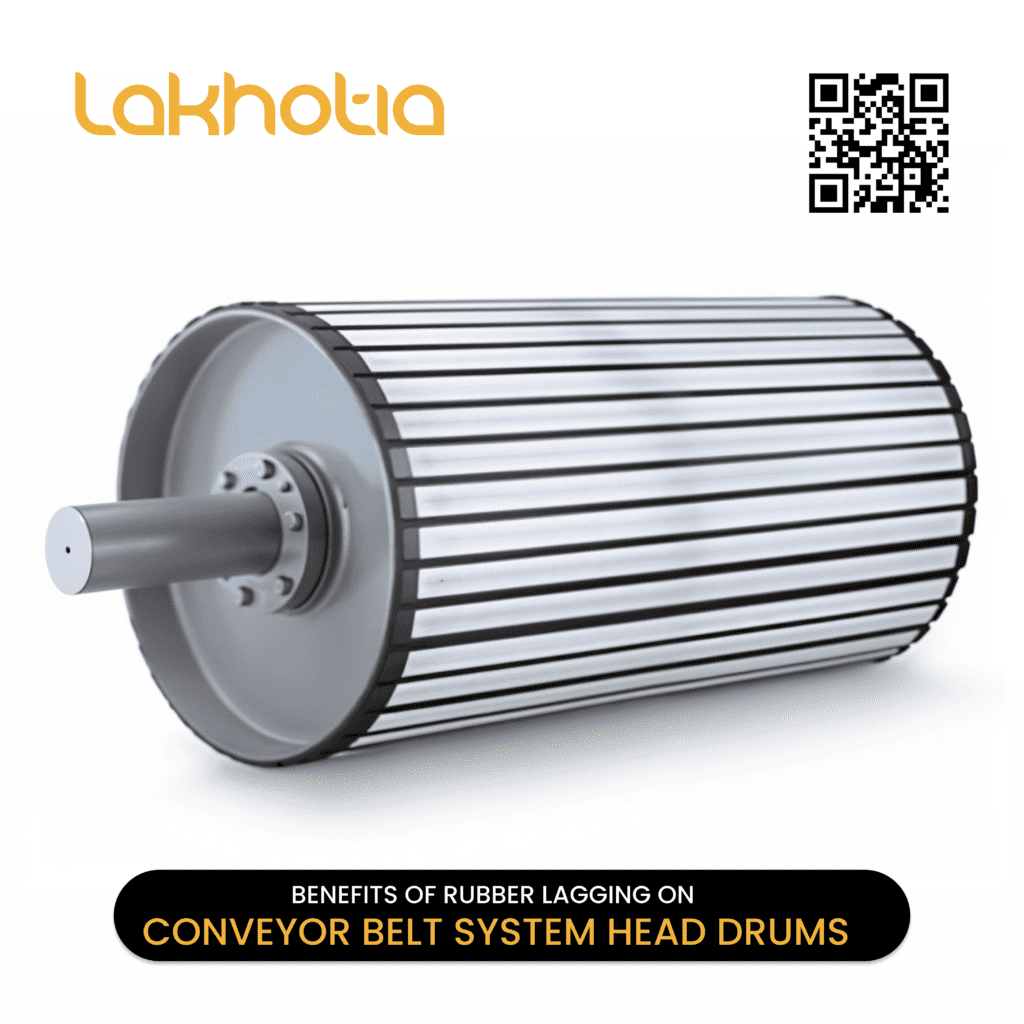
Benefits of Using Lagging Rubber on Head Drums
Conveyor belt systems are the backbone of many industrial operations, handling the transportation of materials efficiently across vast distances. A key component of these systems is the head drum (also known as the drive pulley), which plays a crucial role in transferring power to the belt. However, to ensure smooth and effective functioning, it’s essential to enhance this component with the right materials. One such enhancement is the application of rubber lagging. Rubber lagging on the head drum significantly improves the performance, efficiency, and durability of industrial conveyor systems. It offers a range of advantages, including better traction, reduced wear, and enhanced safety. In this blog, we will explore the benefits of using conveyor pulley lagging on head drums and how it contributes to the overall functionality of the conveyor belt system.
Enhanced Traction:
Rubber lagging is an effective way to improve traction between the conveyor belt and the head drum. This is especially important during the startup phase or when the conveyor belt system is under heavy load. Without adequate traction, the conveyor belt may slip, causing inefficient power transmission and delays in material handling. By applying rubber lagging, this issue is mitigated, ensuring smoother operation and reliable performance, even under challenging conditions.
Prevention of Belt Wear:
One of the most common problems in industrial conveyor systems is excessive belt wear. Over time, friction between the conveyor belt and the head drum can cause significant damage to the belt. rubber lagging for conveyor pulley acts as a protective layer, reducing direct contact between the belt and the metal surface of the drum. This helps minimize wear, resulting in lower maintenance costs and an extended lifespan of the industrial conveyor belt.
Improved Drive Efficiency:
When slippage is minimized by conveyor pulley lagging, the drive system becomes more efficient. The rubber coating helps ensure that the power from the motor is effectively transferred to the conveyor belt, reducing energy wastage and improving the overall drive efficiency. This leads to lower operating costs and better overall energy performance within the conveyor belt system.
Shock Absorption:
Rubber lagging provides a cushioning effect that absorbs shocks and impacts from the conveyed material. During material handling, the industrial conveyor system can experience sudden impacts, which could damage both the belt and the head drum. The rubber surface helps protect these components by absorbing the shock, thereby reducing the risk of wear and tear or system failure in the conveyor belt system.
Effective Discharge of Material:
Many industrial materials tend to build up on the head drum. This can cause operational inefficiencies, such as belt misalignment and material buildup on the drum. Rubber lagging, especially when textured or grooved, facilitates the effective discharge of materials from the industrial conveyor belt. This ensures that the drum remains clean, and material flow is not interrupted, resulting in a more efficient and smooth operation of the conveyor belt system.
Reduced Noise and Vibration:
Conveyor belt systems can often be noisy, and excessive vibration can contribute to operator fatigue and equipment wear. The application of rubber lagging for conveyor pulley helps dampen noise and vibration, creating a quieter and more relaxed workplace environment. This not only contributes to a safer and more comfortable working environment but also helps extend the lifespan of the industrial conveyor belt.
Protection Against Corrosion:
In many industrial conveyor systems, the systems are exposed to corrosive materials or harsh weather conditions. Rubber lagging acts as a protective barrier, preventing direct contact between the head drum and corrosive substances. This helps protect the drum from corrosion, enhancing its durability and extending its service life in the conveyor belt system.
Improved Belt Tracking:
One of the most common problems in industrial conveyor systems is belt misalignment. Rubber lagging helps improve belt tracking by providing a stable, consistent surface for the conveyor belt to move along. This reduces the chances of misalignment, ensuring that the conveyor belt system runs smoothly and efficiently throughout its operational life.
Easy Replacement and Maintenance:
Rubber lagging is relatively easy to install and replace. This feature is crucial for industrial conveyor systems that require frequent maintenance. The ease of replacement helps reduce downtime and allows for faster system repairs, ensuring that the conveyor belt system stays operational without significant disruptions.
Customization Options:
rubber lagging for conveyor pulley is not a one-size-fits-all solution. It is available in a variety of patterns and types, offering customization based on the specific requirements of the conveyor system. Whether it’s a textured surface or grooved patterns, the conveyor pulley lagging can be tailored to meet the needs of different materials and industries, improving the efficiency of the conveyor belt system.
Safety Enhancement:
One of the key advantages of using rubber lagging is its contribution to safety. By improving traction and reducing belt slippage, the risk of accidents related to conveyor belt systems malfunctioning is minimized. Additionally, conveyor pulley lagging helps prevent sudden wear-related failures, which could lead to dangerous breakdowns in the conveyor belt system.
Adaptability to Various Conditions:
Rubber lagging is highly versatile and can be adapted to suit various operating conditions. Whether you’re dealing with heavy-duty industrial conveyor systems or corrosive environments, rubber lagging for conveyor pulley can be tailored to meet the unique demands of your conveyor belt system, ensuring reliable performance across different conditions.
Conclusion
Rubber lagging for conveyor pulleys on head drums is crucial for enhancing conveyor belt systems. It improves traction, preventing belt slippage during start-up and heavy load conditions. Rubber lagging also reduces wear by protecting the conveyor belt from metal contact, extending its lifespan. It absorbs shocks and vibrations, ensuring smoother operations. Additionally, it helps protect against corrosion in harsh environments, ensuring durability. Rubber lagging improves material discharge, preventing buildup on the drum. It also aids in better belt tracking, reducing misalignment. By investing in rubber lagging, industries can boost energy efficiency and reduce downtime. At Lakhotia, we offer a variety of solutions, including bucket elevator belts, heavy-duty conveyor belts, and rubber conveyor belts. Trust us for high-quality products that enhance your industrial conveyor systems.