There are various advantages to applying rubber lagging to a rubber conveyor belt’s head drum (drive pulley) that improve the system’s effectiveness, durability, and safety.Here are some key advantages of using lagging rubber on head drums:
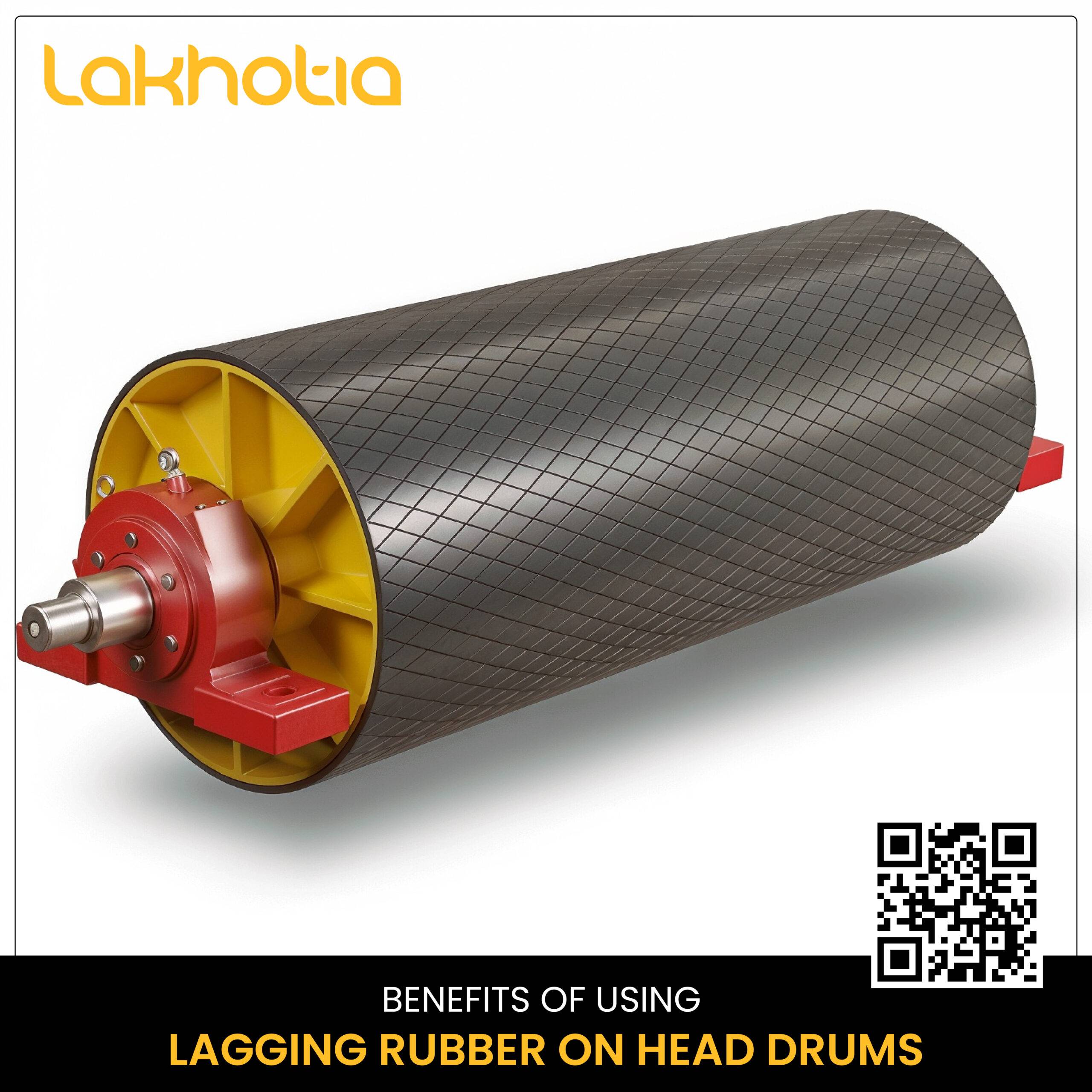
Rubber lagging significantly improves the traction between the rubber conveyor belt and the head drum. This is crucial during start-up and under heavy load conditions, preventing belt slippage and ensuring efficient power transmission.
Lagging rubber acts as a protective layer, reducing the direct contact between the conveyor belt and the metal surface of the head drum. This helps minimize wear and extends the lifespan of the conveyor belt.
Rubber lagging improves the drive system’s efficiency by lowering slippage. It allows for the effective transfer of power from the motor to the conveyor belt, contributing to energy efficiency. This improvement is a key benefit offered by rubber conveyor belt suppliers.
Rubber lagging provides a cushioning effect, absorbing shocks and impacts from the conveyed material. This ensures the durability of the system’s components as well as the conveyor belt’s materials by preventing damage to both the head drum and the belt.
Lagging with a textured or grooved surface can assist in the effective discharge of materials from the belt, preventing material buildup on the drum and ensuring a clean operation. This benefit is often highlighted by rubber conveyor belt suppliers.
The application of rubber lagging helps dampen noise and reduce vibration during conveyor operation. As a result, the workplace may be quieter and more relaxed.
In corrosive environments, rubber lagging acts as a barrier, protecting the head drum from direct exposure to corrosive materials. This helps prevent corrosion and extends the activity of the drum, a key advantage emphasized by rubber conveyor belt suppliers.
Rubber lagging assists in maintaining proper belt tracking by providing a consistent and reliable surface for the conveyor belt to run on. This helps prevent misalignment issues, a benefit often highlighted by rubber conveyor belt suppliers.
Rubber lagging makes maintenance duties easier to do and minimises downtime during conveyor system operations. It is also generally easy to install and replace. This ease of maintenance is often emphasized by rubber belting suppliers.
Rubber lagging is available in various patterns and types, allowing for customization based on specific conveyor requirements. Different textures and grooving patterns can be chosen depending on the application and conveyed material.
By lessening the chance of belt slippage, which can be dangerous, lagging rubber improves safety. It also minimizes wear-related issues that could lead to unexpected failures, a key benefit emphasized by rubber belting suppliers.
Rubber lagging is suitable for a wide range of operating conditions, making it adaptable to different industries, materials, and environmental factors. This versatility is a key feature highlighted by rubber belting suppliers.
At Lakhotia, we provide comprehensive services for all your conveyor system needs, including the application of high-quality lagging rubber for head drums. Our expert solutions ensure enhanced safety, durability, and performance for your conveyor systems. Additionally, we offer a wide range of premium conveyor belts, including bucket elevator belts, heavy-duty conveyor belts, rubber conveyor belts, EP conveyor belts, and heat-resistant conveyor belts, tailored to your specific requirements. Trust Lakhotia for reliable and long-lasting conveyor belt products and services.
In summary, applying lagging rubber to head drums enhances the overall implementation, safety, and durability of belt conveyor systems. It provides benefits such as improved traction, reduced wear, shock absorption, noise reduction, and ease of maintenance. The specific type of lagging rubber chosen can depend on the unique requirements of the conveyor system and the conveyor belt materials being conveyed.